Guide
Engine Blocks
In our offer, you will find engine blocks from well-known brands like BF Germany, Mec Diesel, and MV Parts. Depending on the brand and model of the engine, these can be either Short block or Long block. The blocks may come with fitted cylinder heads, timing, or oil pans. Everything depends on whether a particular engine has only one type of these components.
In this article, we will cover the following issues:
- The role of the engine block
- The weight of an engine block
- Types of engine blocks
- Engine block malfunctions
- Cracked engine block: symptoms
- How to seal a cracked engine block?
- Painting the engine block
Engine block – the role of the part
The engine block, also known as the engine casing or crankcase, is a fundamental part of a combustion engine. It is the part of the engine where the cylinders, pistons, connecting rods, and the crankshaft are mounted. The engine block performs several key functions – its main role is to support the moving parts – the engine block is the structure that holds the moving parts of the engine, such as pistons and the crankshaft, in the correct positions and allows them to operate in a synchronized manner.
The engine block is made of metal, usually cast iron or aluminum, which allows efficient dissipation of heat generated during the fuel combustion in the cylinders. The engine block must be sealed properly to prevent oil or coolant leaks and to maintain the correct pressure inside the cylinders.
In short, the engine block forms the basic structure on which the entire engine mechanics are based, ensuring the necessary durability, sealing, and functionality of the entire vehicle’s powertrain.
How much does an engine block weigh?
The weight of an engine block can vary significantly depending on the type of engine, its size, design, and the material it is made from. On average, an automotive engine block for a standard gasoline or diesel engine can weigh from about 100 to 300 kilograms.
Here are a few factors that influence the weight of an engine block:
- Material: Engine blocks can be made from different materials, such as cast iron, aluminum, or even aluminum alloys with cast iron inserts or other additives. Aluminum blocks are typically lighter than cast iron blocks, which can reduce the weight of the entire engine.
- Size and capacity: Larger-capacity engine blocks are usually bigger and heavier than those with smaller capacity, as they need to accommodate more cylinders, pistons, connecting rods, etc.
- Design: Engine blocks with more advanced designs can be lighter as they may be designed using advanced technologies that reduce weight, for example, using hollow sections, reducing wall thickness, or using composites.
- Type of engine: Engines with different configurations, such as inline, V6, V8, or even W12, will have different engine block weights due to differences in their designs.
Therefore, the weight of an engine block can vary significantly based on these factors. For larger or high-performance engines, the engine block’s weight may be greater due to a higher number of cylinders, increased strength, or the use of more advanced construction materials.
Types of engine blocks
Engine blocks come in various types and configurations, each with its own distinctive features and applications. Here are some of the popular types of engine blocks:
- Inline (straight) block
Inline engine blocks have cylinders arranged in a single line. Inline engines are often used in passenger cars, motorcycles, and other vehicles. They are simple in design, easy to maintain, and cost-effective in production. - V block
V engine blocks have cylinders arranged at an angle to each other, forming a “V” shape. V engines are popular in passenger cars, sports cars, and larger-capacity vehicles like SUVs and pickups. V engines are often more compact and can achieve higher power outputs compared to inline engines. - W block
W engine blocks have cylinders arranged at an angle to each other in such a way that they form a “W” shape. This type of block is mainly used in high-capacity engines, including some sports cars and high-performance vehicles. - Boxer (flat) block
Boxer engine blocks have cylinders opposed to each other so that the pistons move in opposite directions. Boxer engines are characteristic of certain brands, such as Porsche and Subaru. With their low center of gravity and even weight distribution, boxer engines offer certain advantages in vehicle handling. - Rotary block
Rotary engine blocks, also known as Wankel engines, have an unusual design with a rotating rotor instead of traditional pistons and cylinders. Rotary engines are relatively lightweight and compact, making them popular in ultralight aircraft, motorcycles, and sports vehicles.
The choice of a specific type of engine block depends on the specifications of the vehicle, its purpose, performance, and the manufacturer’s preferences. Each type of block has its advantages and limitations, which must be considered during the design and production of the engine.
Engine block malfunctions
Common engine block malfunctions can arise from various factors, including improper maintenance, mechanical damage, or material defects. However, wear and tear is the most common cause. Frequent malfunctions include:
- Cracks: The engine block can crack due to extreme operating conditions, sudden temperature changes, or too high internal pressure. Cracks can lead to coolant leaks, oil leaks, or even structural damage.
- Piston seizures: Wear or damage to the cylinder surfaces can cause piston seizures in the cylinder, resulting in power loss, engine noise, or failure.
- Deformations: In cases of strong shocks, impacts, or improper loading, the engine block can deform, affecting its performance and sealing.
- Corrosion: Corrosion can occur due to prolonged exposure to moisture and salt on the engine block, especially if the vehicle is operated in areas with aggressive atmospheric conditions.
- Damage due to overheating: Overheating can cause damage to the engine block, particularly in engines made of aluminum, which may be more prone to deformation and cracking under extreme temperatures.
It’s worth noting that engine block repair can be costly and complex, depending on the extent of damage and the type of engine. In some cases, replacement of the entire block may be required. Therefore, regular maintenance, ensuring proper engine operating temperatures, and avoiding excessive loads can help prevent serious engine block malfunctions.
Cracked engine block: symptoms
A cracked engine block can manifest in various symptoms, depending on the location and size of the crack and its impact on engine functioning. Here are some possible symptoms of a cracked engine block:
- Fluid leaks: A crack in the engine block can lead to fluid leaks, such as engine oil, coolant, or hydraulic fluid. These leaks may be visible under the vehicle or around the engine area.
- Decrease in fluid levels: If you notice a continuous decrease in fluid levels in the reservoirs, like the oil or coolant tank, it could be a sign of a leak caused by a crack in the engine block.
- Unusual sounds: A cracked engine block can lead to abnormal sounds, such as knocking, banging, or buzzing, when the engine is running. This may be due to improper movement or contact of components as a result of the block’s deformation.
- Loss of power: In cases of larger cracks that affect the pressure in the cylinders or the movement of pistons, the engine might lose power or exhibit irregular operation.
- Piston seizures: Cracks in the area of the cylinders can lead to piston seizures, resulting in decreased compression, loss of engine power, and internal noises.
- Increase in temperature: A cracked engine block can lead to improper cooling of the engine, which may manifest as an increase in engine temperature on the temperature gauge or alarms indicating engine overheating.
If you experience symptoms and suspect a cracked engine block, it’s essential to diagnose the problem promptly and undertake appropriate repair actions to avoid more severe damage or failure. In such cases, a visit to an automotive workshop is usually necessary, where a mechanic can thoroughly examine and assess the condition of the engine block.
How to seal a cracked engine block?
A serious mechanic asked this question would respond – can it really be sealed/glued? Repairing a cracked engine block can be complicated and often requires specialized tools and experience. In cases of severe damage, it is advisable to consult a professional mechanic or a specialized engine workshop. Here are some methods for repairing a cracked engine block:
- Welding: In some cases, especially when the crack is relatively small and easily accessible, welding the cracked part of the engine block may be possible. However, welding an engine block can be complicated and requires specialized knowledge and skills, especially if the block is made of aluminum.
- Injection of epoxies or resins: There are special epoxies and resins that can be used to inject into cracks in the engine block to seal them. However, this method can be difficult to apply for large or deep cracks and may not be durable under heavy engine loads.
- Sealing cracks with specialized sealants: There are special crack sealants that can be applied to seal cracks in the engine block. However, the effectiveness of these products can vary depending on the type of crack and operating conditions.
- Replacing the block: In cases of severe damage that cannot be effectively repaired, the best option might be to replace the engine block with a new or refurbished one.
Regardless of the chosen repair method, it’s important that the repair is carried out by a qualified and experienced mechanic or workshop with the right tools, knowledge, and skills to perform the repair safely and effectively. Additionally, always consider the repair costs compared to the value of the vehicle to decide whether repairing a cracked engine block is cost-effective.
Painting the engine block: why and how to paint
Why paint the engine block?
Painting the engine block is an important process mainly from the perspective of its protection. The engine block, being exposed to environmental conditions and high temperatures, requires a special finish that ensures its durability and maximum efficiency.
Protection against corrosion is one of the main reasons for painting the engine block. The metal surfaces of the block are prone to corrosion caused by moisture, road salt, and other external factors. Painting creates a protective barrier that prevents rusting and the formation of corrosion on the block surfaces.
Additionally, properly chosen engine block paint can also improve thermal performance by dispersing heat. Some paints have thermal properties that help in dissipating excess heat from the engine, which can contribute to better cooling system performance.
What to use to paint the engine block?
Painting the engine block requires the use of special paints that are resistant to high temperatures, oils, fuels, and other chemical substances present in the engine’s working environment. Here are some popular paint options for painting engine blocks:
- Thermal insulating paints: Thermal insulating paints are designed for surfaces subjected to high temperatures, making them suitable for painting engine blocks. Such paints can help in dispersing heat, which can be useful in limiting engine heating. Thermal insulating paints are also resistant to corrosion and chemicals.
- Engine paints: There are special paints dedicated to painting engines and engine blocks. These paints are designed to provide durable protection against high temperature, corrosion, oils, and other chemicals found in the engine environment.
- Ceramic paints: Ceramic paints are very durable and resistant to high temperatures, making them suitable for painting engine blocks. Ceramic paints can also help reduce heat emissions, which can be beneficial for engine performance.
- Epoxy coatings: Some epoxy coatings are resistant to high temperatures and can be used for painting engine blocks. These coatings also have good resistance to oils, fuels, and chemicals.
Before painting the engine block, it is important to properly prepare the surface by cleaning it of dirt, rust, and old paint. Then, carefully apply the chosen paint according to the manufacturer’s instructions, ensuring the appropriate thickness and even coverage of the engine block surface.
Podobne wpisy
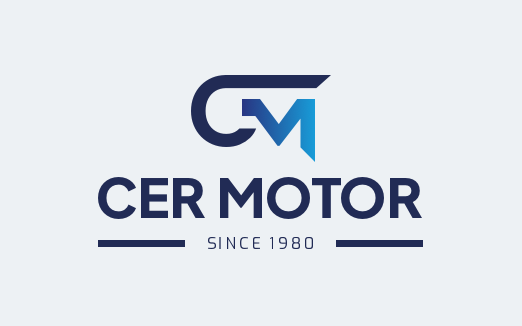
Piston Rings
Piston rings are made from spheroidal (gray) cast iron or steel. Steel rings are differentiated into chromed with a martensitic […]
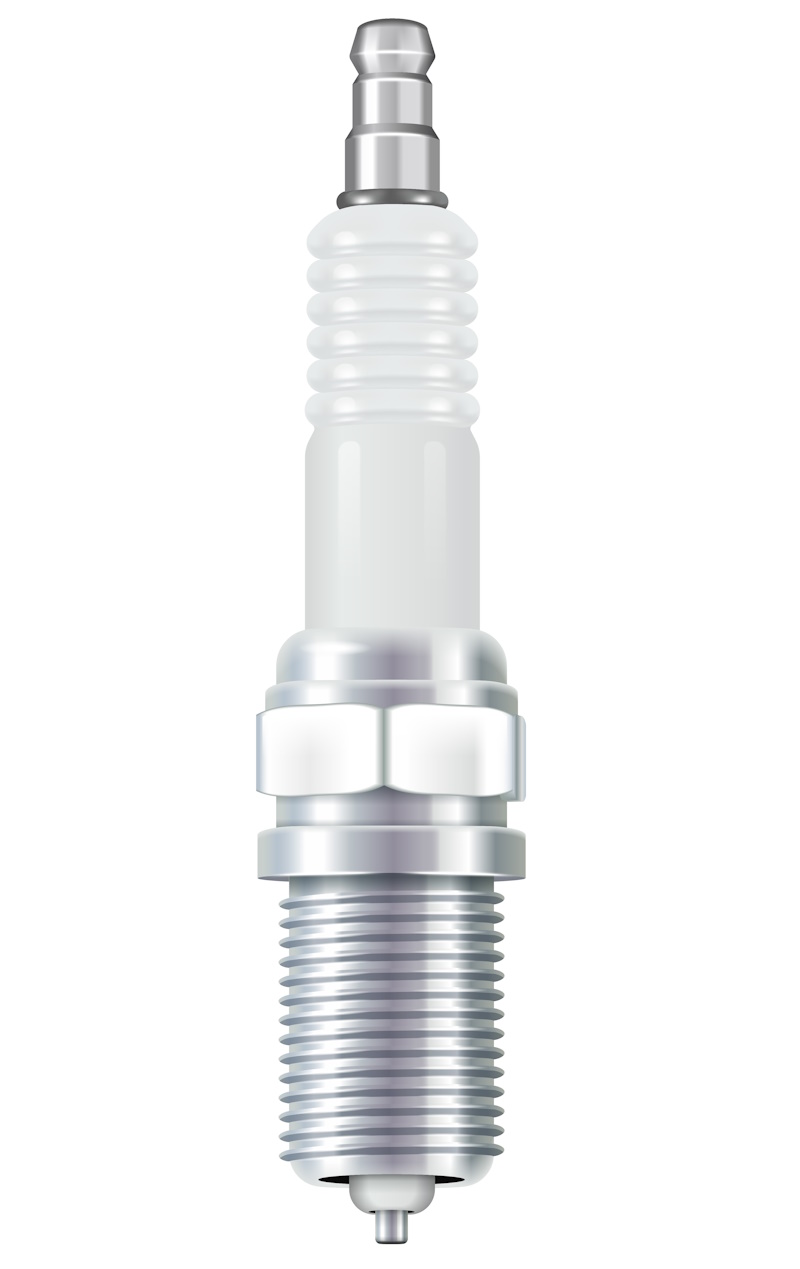
Spark/Ignition Plugs
A spark plug is a fundamental and one of the most important components of the ignition system. Its condition affects […]
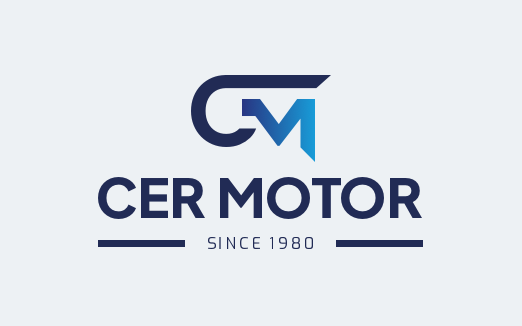
Intake and exhaust valves
Intake and exhaust valves isolate the combustion chamber and optimize gas exchange. Being in continuous motion – and under harsh […]